Getting the most out of flap wheels
Not sure which flap wheel is right for you? Should you use a coated abrasive flap wheel, combi, or a non-woven flap wheel? See the different types and what they are best for, and use this guide to match up your desired result with the best flap wheel for the job.
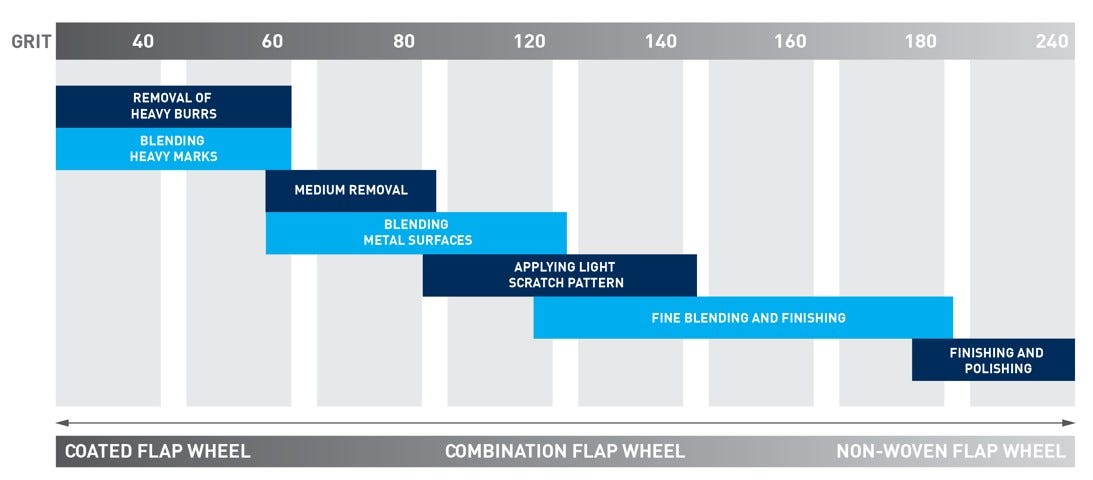
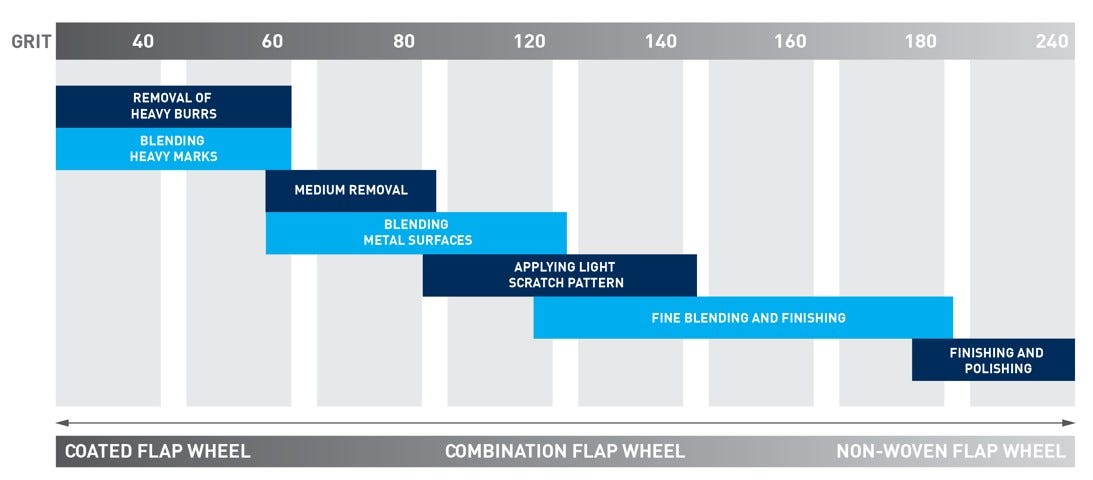
Coated flap wheel (standard sandpaper flap wheel)
(standard sandpaper flap wheel)
Best for heavy to light removal like; weld removal, deburring, and blending, to give a consistent cut rate, and uniform grain finish (light line finish). Grits from P40 - P400
Able to be use on all metal, including stainless steel, and aluminium.
Sizes are come in 20 - 60mm on spindle mounted. Or 100 - 165mm Large wooden centre flap wheels.
Combination flap disc
(Combination of sandpaper and non-woven (scotch bright) abrasives flaps)
Less aggressive than the standard flap wheel, use for applying a light pattern or fine blending, and finishing.
Provides a more of a brushed/satin finish rather than a grain finish (less stand-out lines). Medium to fine grits.
Available in small spindle mount or larger taper centre wheels.
Non-woven flap wheels (scotch bright type cloth)
For light cleaning and a fine satin finishing on Stainless Steel. Coarse-Fine grits
Available in small spindle mount or larger taper centre wheels.
Corrugated wheels (Non-woven type cloth in corrugated form, not flaps)
Best used when a satin finish is required on stainless, chrome, nickel and non-ferrous metals.
Less line marks from side of wheel, unlike standard Flap wheels wheels.
The flap wheel finish
All photos are on the same #3 stainless steel finish.
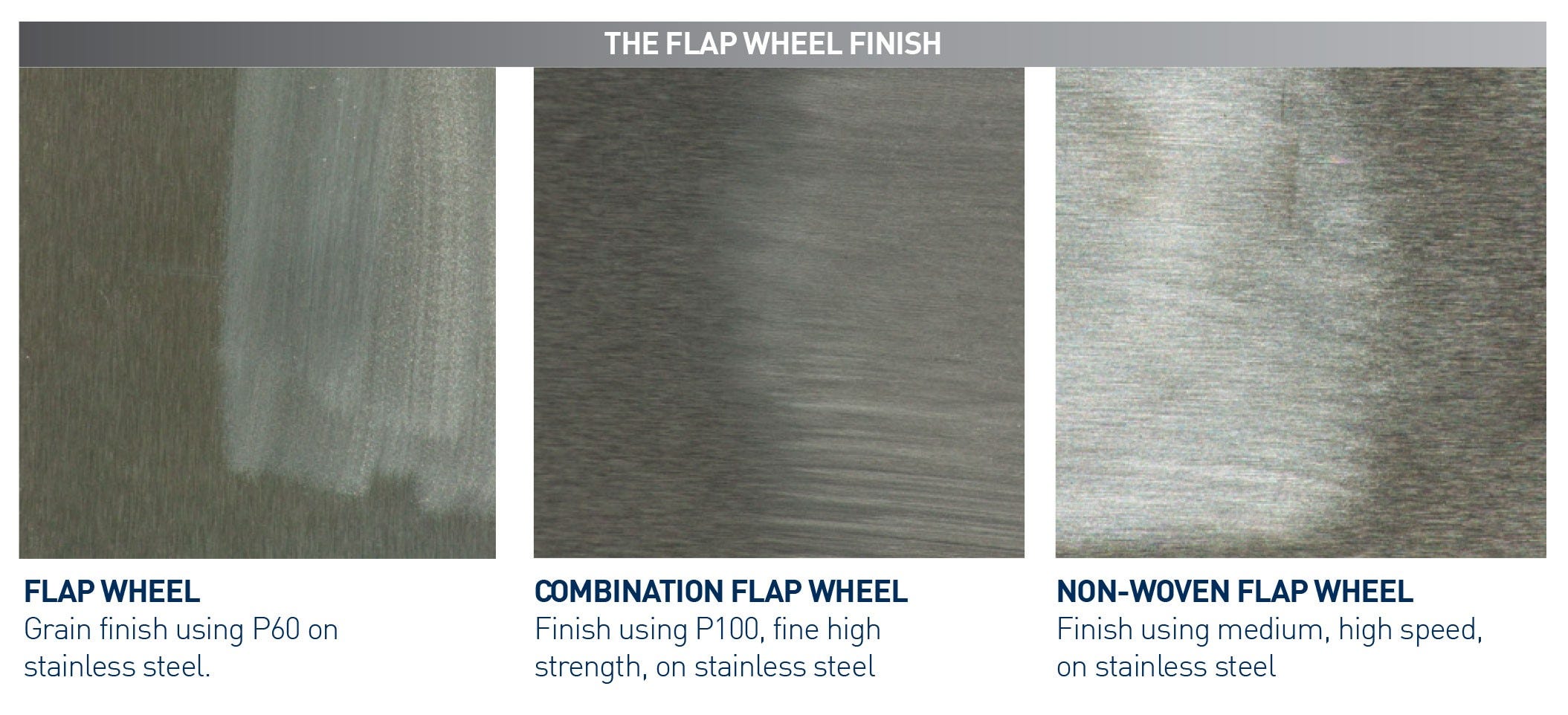
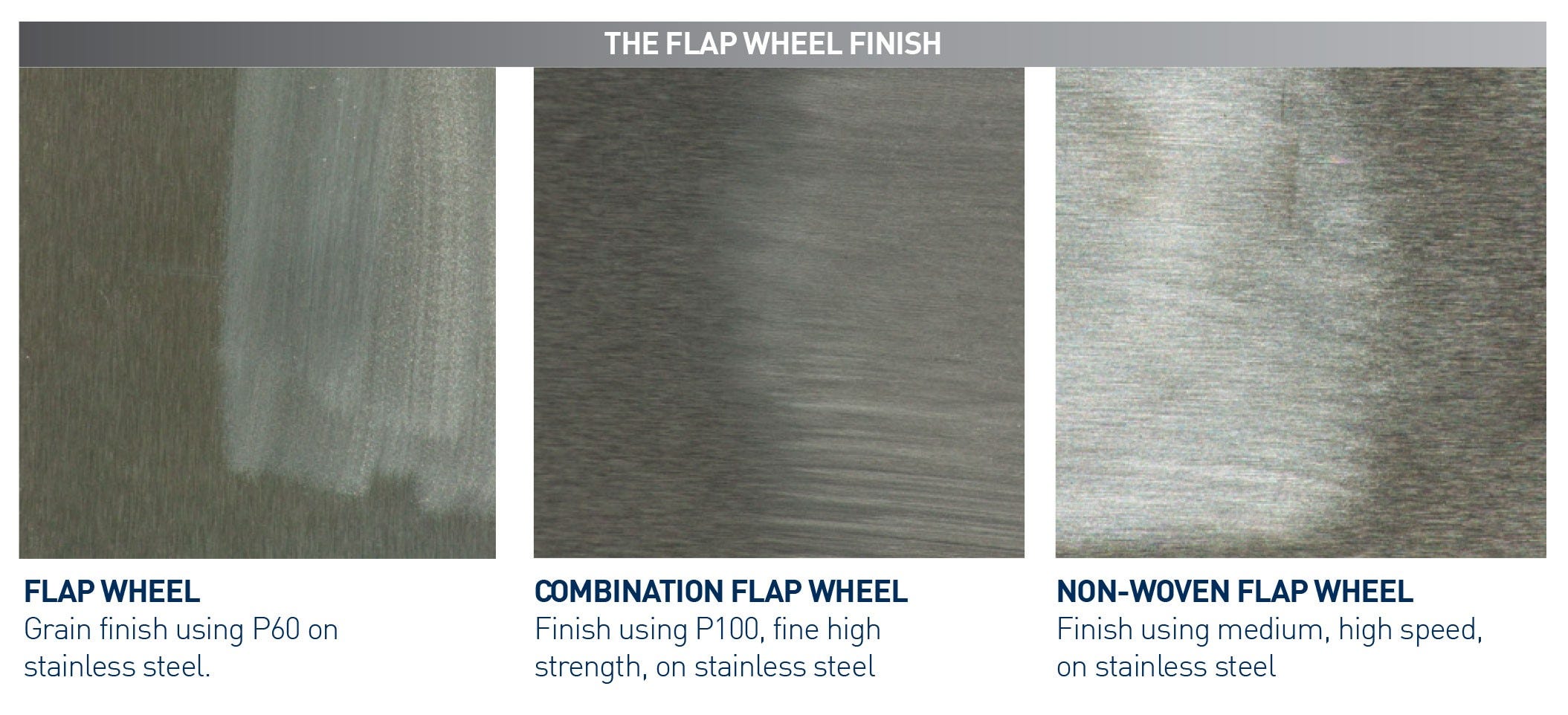
If you haven't tried any flap wheels yet, or maybe have but just want to remove stock faster, or just trying to get a different finish we recommend you start trying now. With the 4 variables above there is a solution for most fabrication applications.
See the different types available here.