Kanban vs Min/Max – What’s Best?
When managing consumable stock in house the method you use to control stock levels can be critical. Did you know inventory carrying costs can be as much as 20-30% of your total inventory costs? That’s a pretty good reason for keeping an eye on what’s being ordered. Plus having a process to follow can just make your job a whole lot easier.
Kanban and min/max are two of the most popular methods of inventory control, before we get into which one might be best for your workshop, here’s a little more info around inventory control methods…
What is an inventory control method?
Inventory control methods are processes used to optimise the amount of stock being held in your workshop. It allows the inventory manager to easily identify what product needs to be ordered, and how much should be ordered to maintain a target level.
Why use an inventory control method?
Due to the high cost of carrying excess inventory, many workshops choose a lean approach to inventory management where the stock held is directly related to the amount required to keep production moving. Aside from a small buffer amount of stock, this means inventory being stored on site is kept at a minimum, thereby keeping carrying costs low.
Inventory control methods are not just useful for keeping better control over your stock levels, but having a process often helps to streamline the ordering process for the inventory manager.
When to implement inventory control
Inventory control methods like Kanban or min/max can be utilised in any workshop stocking regularly used/ordered consumables. These systems will have most benefit for products being ordered on a frequent basis, such as weekly, fortnightly or monthly.
Kanban vs Min/Max
Kanban Two Bin Method
Kanban’s two-bin system splits consumable stock into two ‘bins’. The quantity in each bin should be enough to keep production flowing until the next ordering cycle (eg. 1 week/month worth of product). Once product from the first bin is used, the second bin gets brought forward for product to be taken from. The empty first bin then gets put in an area for re-ordering. When it is time to place supplier orders, the inventory manager can easily see what needs ordering and the quantities needed from the empty bin boxes left in the re-ordering bay.
Min/Max Method
The min/max system is the most simple inventory control method. Minimum and maximum stock quantities are determined based on the minimum amount needed to keep production moving until an order can be placed and delivered, and a maximum being the average amount used throughout an ordering period (eg. 1 month) + the minimum value – this provides a buffer to prevent stock runouts.
Pros
- Minimal stock needs to be held on site.
- Good visibility of ordering requirements.
- Minimises risk of stock runouts.
- Increased inventory management efficiency.
- Reduced capital requirements from lower stock holding.
Pros
- Quick to set up.
- Minimises risk of stock runouts.
- Improved inventory management efficiency.
- Reduced capital requirements from lower stock holding.
Cons
- More time required to set up than Min/Max.
- More frequent purchase orders required.
- Requires in-house management of inventory.
- Staff need to be trained and monitored to ensure the system is being used.
- Cash still needs to be tied up in stock.
Cons
- Still requires inventory to be counted to determine if an order needs to be placed, and how much.
- More frequent purchase orders required.
- Requires in-house management of inventory.
- Cash still needs to be tied up in stock.
So which method is best?
It really depends on the size and processes in your workshop as to what would work best for you. The Kanban Two Bin method has the advantage of being a lot faster for placing purchase orders once set up, because there’s no counting involved. However, the Kanban method could be a bit of an overkill for smaller workshops that simply don’t have that much stock to keep track of. So keeping in mind the more products you need to order, the more time you’d be taking to count your stock levels, we’d suggest Kanban for workshops carrying a lot of regularly ordered consumables, and Min/Max for those with less.
How can I speed up the ordering process?
Look for ordering systems that will streamline your processes, like utilising a favourites list on your suppliers website, or a system like QUICKSCAN where you simply use your mobile phone to scan the barcode of the product that needs ordering and enter the quantity required. Not only do these systems strip back the time required to process a purchase order, but they minimise the chances of ordering errors compared with phone or emailing.
An alternative option
If you really want to trim the fat when it comes to your inventory management time and costs, a supplier managed inventory system like QUICKSTOCK™ is proven to do just that. The supplier will hold stock on site, manage the inventory levels, and you only pay for what is used each month – so your cash isn’t tied up in inventory, AND you don’t have to spend time counting stock and placing orders! Find out more about QUICKSTOCK here.
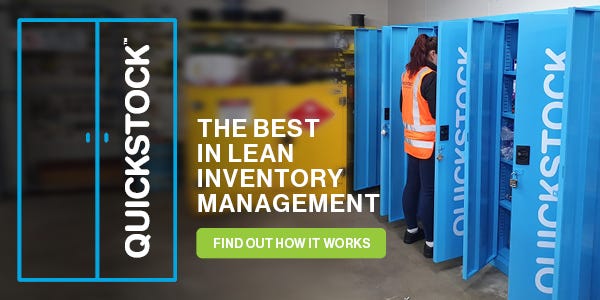
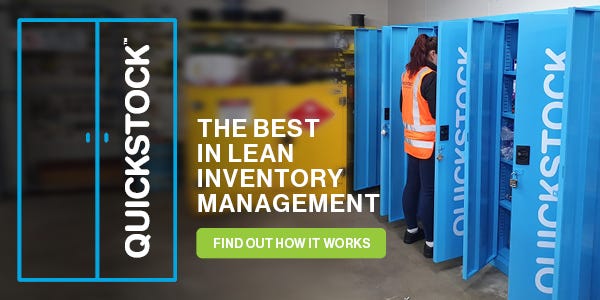